A Practical Guide For Evaluation Of Automation Systems In Feed Industry
In order to select an automation system for a feed factory we need common criteria to compare offers from different vendors. A list of common criteria will enable us to see features we need in an automation system and features unnecessary for us. We can also compare purchasing price, operating and maintenance costs of the offers. In this article we present the most common characteristics of automation systems used in the feed industry that we hope will help purchasing decisions.
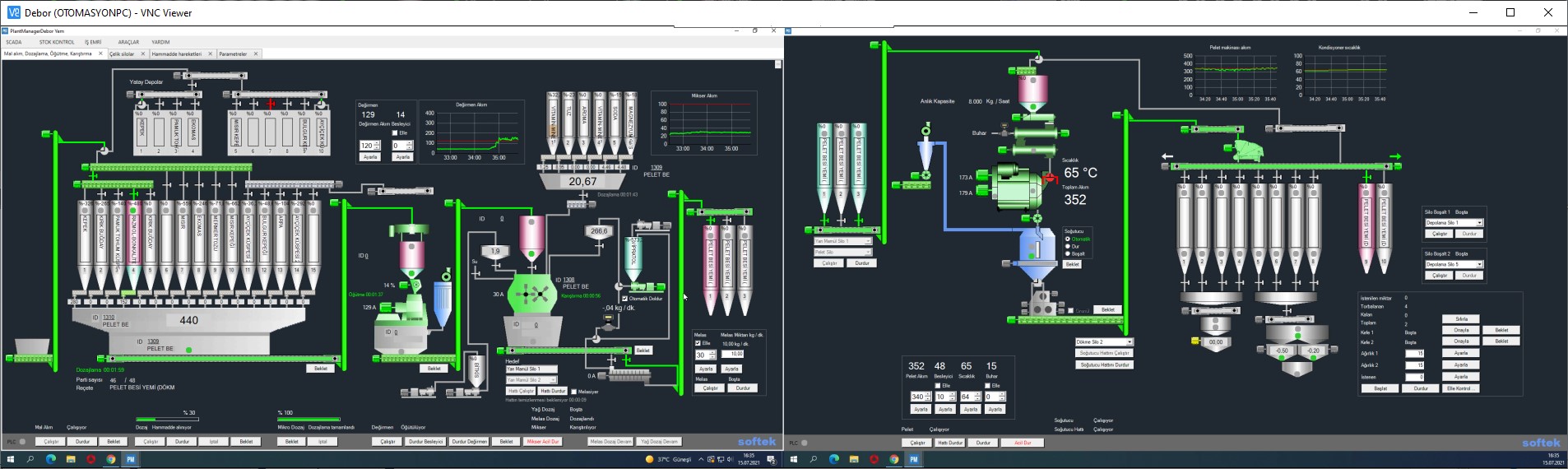
1- PLC/Controller
PLC’s evolve continuously. New models with new features and more capacity are introduced and old models are discontinued. For maintenance and extension of the automation system, it is imperative that PLC used in the system will be supported by the manufacturer in a reasonable time frame. In the case of the PLC vendor discontinuing manufacturing and support, there must be compatible replacement. We also need to make sure that parts such as input/output modules are easily available in the market.
2- User Interface And Visualization
An automation system has a user interface. Users interact with the system through user interface and it contains visualization of the mechanical structure of the factory. Visualization must be consistent and meaningful. It should indicate the state of the system in an easily understable manner. It should indicate important events in noticable form. For example, indication of mechanical failures in red color is one way of achieving this. For user interface there are two basic client platforms available at present. Web browser based clients and native clients. Browser clients offer easy maintenance of the software. But native clients are more user friendly and have better user interfaces. Mobile access to the system offers remote employees to interact with the system. A sales representative visiting a customer can check stocks and production schedules through his/her mobile phone. Production manager will receive alarms from the mobile phone and even act on the alarm remotely.
3- Processes
In general, feed production involves following processes.
- Dosing
- Grinding
- Mixing
- Liquid addition
- Pelleting
- Extrusion
- Oil, aroma coating
- Packaging
4- Full Automation
Operators should minimally intervene with the system. Selecting a manufacturing order and destination silo/bin and starting it should be enough for the production to be completed. For processes requiring regulation of variables such as pelleting, only the set points should be set by the operator and the system should be able control the processes fully automatically. Operators should not need to adjust feeder speed manually. Full automation is possible but in practice many systems lack full automation. Full automation is important because it affects the capacity of the process. Since operators can not attend to process all the time if they are needed for manual adjustment they leave a level of margin from the full capacity of the machines. This will prevent using machines in full capacity. The fully automated system on the other hand can attend the process all the time and be able to use the machines in full capacity. Dependence on the operator skills and experience is not desirable since operators might change. Also human intervention is error prone.
5- Traceability Support
Traceability requirements are increasingly becoming important. Traceability is an important tool for prevention of infectious diseases. For this reason, increasingly more strict traceability requirement regulations are imposed. Traceability is also important for quality control and thus customer satisfaction Traceability can be implemented manually but manual methods are error prone and labor intensive. Automation can support traceability and ease manual processes to different degrees. Ultimately each unit of the feed produced should be related to raw material information that is included in that unit. Barcoding support in the automation system is an important way of traceability support. For each batch produced a unique identifier should be assigned by the system.
6- Reporting
The system should not only provide process control but also be able to provide useful reports such as: The amount of production for each product. Dosing information for each batch including required amount, dosed amount, error. Tracing information relating products to raw material sources. Trends such as current, heat, feeder speed for pelleting, grinding and other processes involving analog variables. A log for important events such as motor and routing component (e.g. slide gates) failures, dosing errors and others. Audit information for recipes and manufacturing orders.
7- Customizability Through Parameters
Many processes require parameters. In a route comprising conveyors and elevators, starting and stopping of each motor in the route should have waiting time of the previous or next motor. There are set points for current and heat for pelleting, error limits for dosing. These parameters should be accessible by the authorized user and can be changed according to the needs.
8- User management
Different functions of the system are subject to different authorization. For example, entering recipes into the system, entering manufacturing orders and production of manufacturing orders needs to have different authorization. In order to achieve that the system must have: adding, updating deleting of user account with passwords assignment of the authorization It is usually to log various activities with user information. Who was responsible for the production of each batch is an important report that the system provides.
9- Integration With ERP Systems
Recipes and manufacturing orders might be created in an ERP system. Instead of manually entering them into the automation system it is better to import them. The following is a list of other possibilities for integration. Purchase orders Invoices Inventory records The automation system should be open to integration. Today integration is generally achieved using web services.
10- Ability to Work In Ihe Internet
The Internet provides a ubiquitous platform for communication all around the world. The internet provides a cost-effective way to use the system in different locations. Production and management facilities might be located in different locations. A system that is capable of allowing users to be in different locations through the Internet is preferred. Security of the internet must be maintained. Performance and speed of the system should be good enough when used through the Internet.
11- Maintenance And Support
Time is money, especially in a production environment. A failure in the system must be promptly fixed otherwise production stops which is a disaster for the enterprise. 24 hour 7 day support must be available. Remote support must be implemented so that in case of failure the situation can be attended immediately. The internet and VPN is one way of achieving remote support and maintenance. A comprehensive support and maintenance contract must be maintained with the automation system vendor. Database should be backed up regularly.